金华不锈钢轧辊厂家
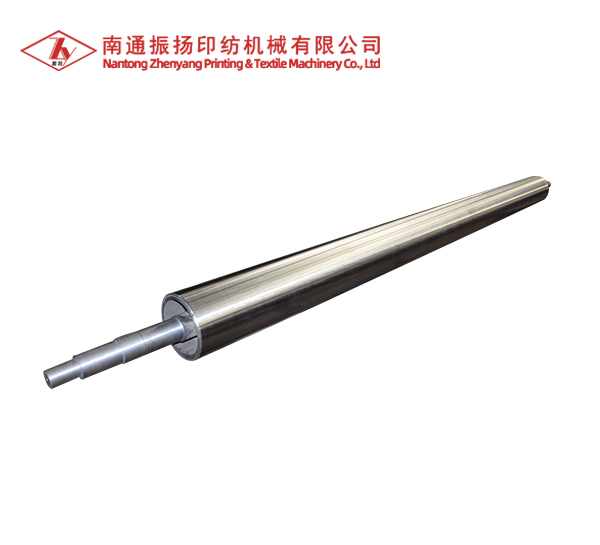
车间环境堆胶辊的影响在闷热和潮湿的天气和来自周围的灰尘飞扬的环境生产中,机器的高速运转使到胶辊的表面温度不断升高,胶辊在发热膨胀,加大胶辊的磨擦,这样会使得胶辊的使用寿命缩短。胶辊之间的压力过重胶辊之间的压力重,会增加胶辊之间的摩擦力,使胶辊升温发热,加重胶辊之间的挤压膨胀,加速胶辊的老化和变形,导布辊加快油墨和水的乳化过程,这样不利于油墨的传递。解决的方法就是:胶辊之间的压力应该和接触版面的压力基本一致。擦洗后,再用干净的布擦一遍然后把胶辊装到机器上,以利下次使用。
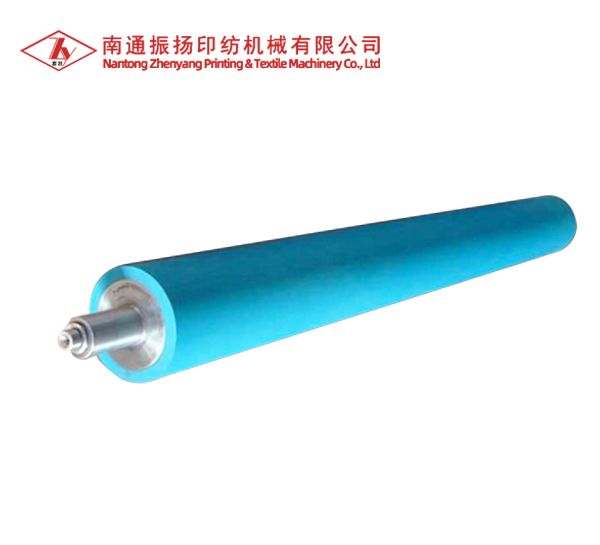
在印刷过程中,油墨中的连接料中的有机物无机物,以及润版液中的亲水胶体,纸张中的脱落的填料,涂料会在墨辊表面形成一层“亮膜”,使得墨辊表面玻璃化,传墨性能下降。除了受热的原因外,主要的原因是使用了不当的清洗剂,使得胶体发生了溶胀。分丝辊解决办法是选择适当的清洗剂(常使胶辊溶胀的有机溶剂:MEK甲基乙醛酮、三氯乙烯、丙酮、环甲烷、香蕉水;不溶胀的有机溶剂:酒精、煤油、轻油、辊清洗剂)。铬辊表面吸附润版液后能使油墨充分隔离,但是过量的润版液,润版液的酸性过强都会加大油墨的乳化,乳化后的油墨会随着回水路返回到水斗辊上,水斗辊上吸附油墨后会造成润版不良,局部水小的故障。必须及时清除水斗辊辊件上的油墨,同时调节润版液量的大小和其成分。
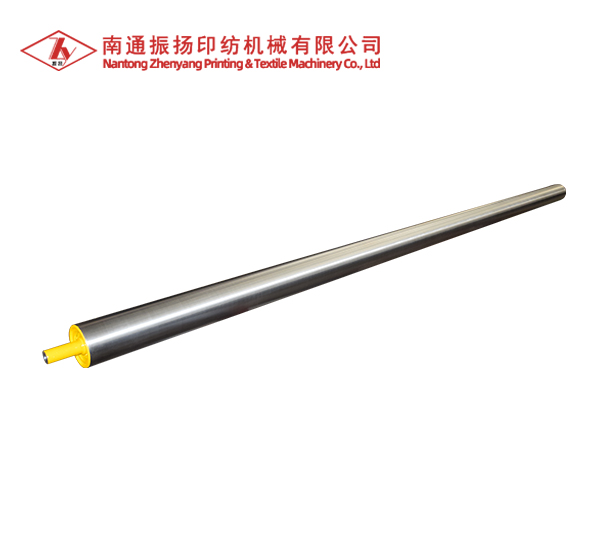
提高工作辊的使用寿命:国外的研究结果是可提高使用寿命2~3倍,这是由于普通辊的抗事故能力比镀铬辊差,辊面容易被带钢勒伤或划伤,并受带钢宽窄限制的缘故。减小工作辊表面粗糙度的下降率:试验的结果是镀铬辊上、下辊表面粗糙度的下降率分别为37.8%和39.7%,而普通辊分别为77.0%和73.0%。减少带钢表面粗糙度的下降率:试验的结果是镀铬辊轧制的带钢上、下表面粗糙度的下降率分别为6.3%和5.9%,而普通辊轧制的分别为42.3%和41.5%。不受带钢宽窄变化的限制,可实现自由轧制。获得更加均匀一致的带钢表面光洁度,带钢喷漆后具有较高的光亮度。
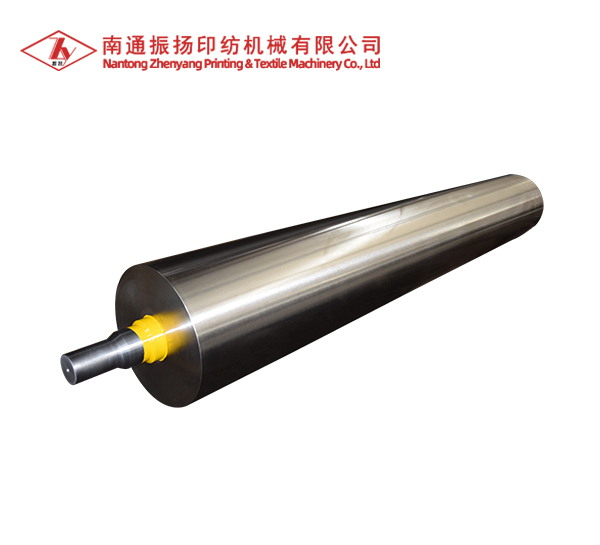
胶型和硬度对于不同的印刷方式来说都是非常重要的,不同的印刷要求胶辊具有不同的机械标准和化学标准。以胶印为例,硬度在一定程度上可反映橡胶的品质,硬度过大可能使其抗腐蚀能力得到一定增强,但是带水和带墨能力下降,并且对于印刷机器的损耗以及对于PS版的图文的磨损增加。硬度过小则可能因抗压和耐腐蚀的能力差而造成胶辊使用寿命过短。确定硬度的原则是:在要保证良好的上水和上墨能力,且有足够的抵抗化学腐蚀和物理作用能力的前提下,印刷胶辊的硬度应适当的降低。在实际印刷应用中,选用适当的胶型可避免由于胶辊的原因引发的印刷质量故障,以保证印刷相对稳定顺畅。
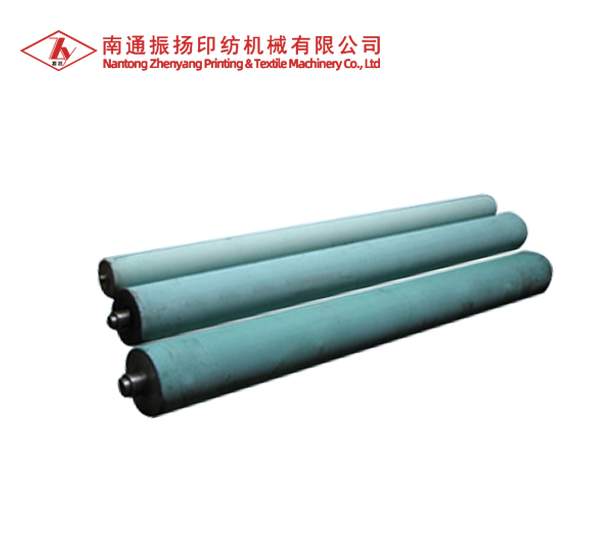
新铸制的胶辊辊件不宜马上投入使用由于新铸制的胶辊内部结构还不够稳定,若立即投入使用,容易降低使用寿命。故刚出筒的新胶辊应放置一段时间,使导布辊接触外界环境温湿度后,保持相对的稳定状态,这样可以增加胶体的坚韧性,从而提高耐用效果。天气寒冷时,油墨打不匀,可适当在油墨中添加辅助材料,禁止用红外线取暖器等设备烘烤油墨胶辊,防止胶辊氧化。胶辊轴头、轴承应保持良好的润滑胶辊轴头、轴承的精度直接影响到传墨、布墨的效果。若润滑不良引起胶辊轴头,轴承的磨损、间隙,必然导致印刷墨色不均匀的弊病。分丝辊同时也会因跳胶、滑胶等不良情况引起印刷杠痕。所以,平时应勤给胶辊轴头、轴承加注润滑油,以防止机件磨损胶辊的正常使用,确保印刷质量。
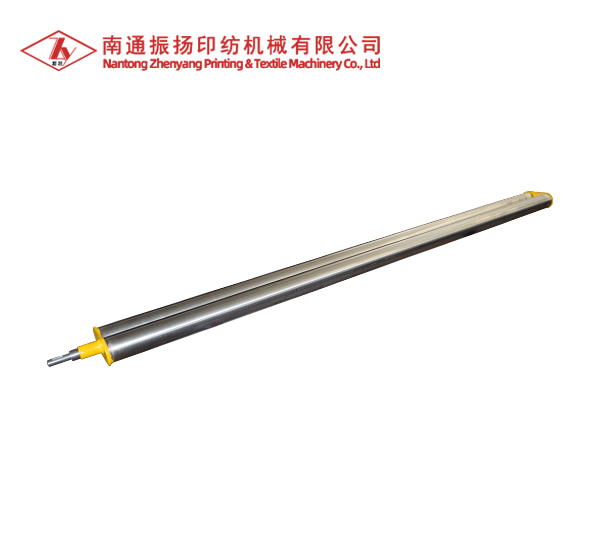
对胶辊来说,胶料的混炼是关键的环节。胶辊用胶料种类从天然橡胶、合成橡胶到特种材料多达10余种以上,含胶率为25%~85%,硬度为(0~90)度,跨越极大范围。因此,如何使这些胶料混炼均匀已成为一大难题。辊件常规的方法是采用开炼机以多种母炼胶的形式进行混炼加工。金华轧辊胶辊成型主要是在金属芯上粘贴包覆橡胶,有包贴法、挤出法、模压法、注压法和注射法等。目前国内主要以机械或手工粘贴成型为主,国外多数已实现了机械自动化。目前,大中型胶辊的硫化方式依然是硫化罐硫化,虽然柔性加压模式有所改变,但仍未脱离往返运输吊卸的繁重劳动负担。导布辊硫化热源有蒸汽、热空气和热水3种加热方式,主流仍是蒸汽。